- Apr 30, 2021
- 2 min read

Did you know PTR manufactures Solar Power equipment?
As an industry leader, we’re continually striving to leverage advancements in technology. Our Solar Power option provides an environmentally-friendly alternative to powering equipment. By utilizing energy from the sun, you’ll see significant savings with installation and operating costs.
Our model Polaris Power System solar power option enables your organization to take a critical step in becoming a universal green energy. If your company has “green” goals, this is a great way to get there! Solar Power helps protect our environment, as well as our economy as we move into a future.
The Polaris Power System provides a complete integrated solution of powering your waste equipment. It can be a stand-alone power source that requires NO external power. Or, it can be used as a hybrid energy option. With the latter option, you would need the support of an alternate 120 VAC charging configuration.
PRIMARY COMPONENTS
The primary components of the solar power option include:
• Two 42 volt PV Photovoltaic Solar Panels,Each rated at 350 Watt. This converts sunlight into DC for powering and charing the machine.
• 6KW inverter with built in AC charger and built in Solar MPPT charger.
• 48 VDC 120Ah Battery Pack. This stores energy potential for machine power.
• Auxiliary Power to run the compactor. There are 2 option here. The first requires the operator to install a 120VAC 30Amp power line. The second line provides a 100ft plug in cord that can be powered by an 15amp convenience outlet for supplemental charging.

Solar options are based on power requirements and intended use with consideration to frequency of use, number of cycles and recovery time to charge. First, we’ll determine the total power requirements of the machine and then size the capacity of the solar option with regard to the number of cycles.
The Polaris Power System includes an intuitive, easy to use touch screen to serve as the local HMI (Human Machine Interface). System health can be determined quickly and easily based on status conditions including Low Battery Level Alarm, Battery Voltage, Battery Temperature, and many more.
The solar option is usually provided as a factory option and mounted directly to the compactor. Note that if the solar option is provided as a hybrid option, you may need provision of a 120 VAC receptacle at 30 amps.
It’s important to consider that even partial shading of the PV panels can significantly hinder the system’s performance. Ensure that the panels will be completely exposed to sunlight to get optimal performance!
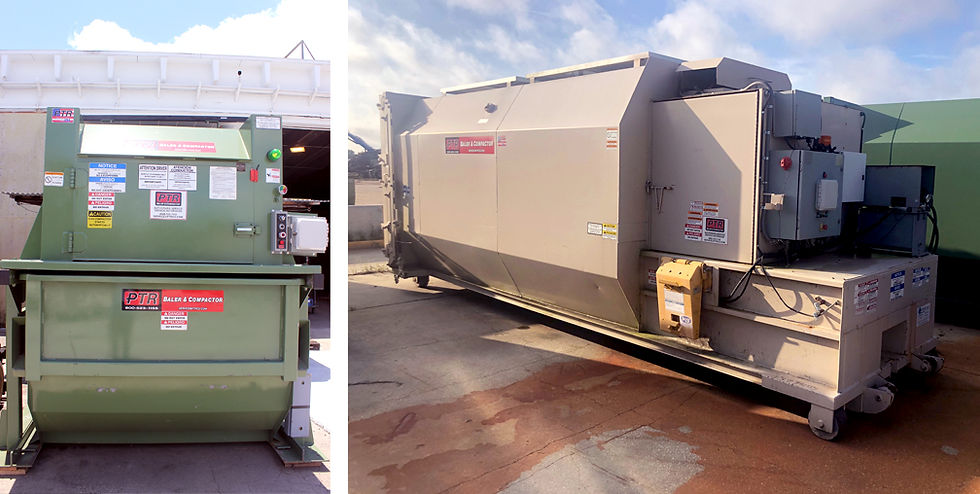
Pictured are the PTR Solar Power Self-Contained Compactor and Solar Power Vertical Compactor. There’s lots of in depth information available, so contact us to learn more or request to be sent a complete manual.
(800) 523-3654