Don’t Let the Holidays Scare You!
- vstarushchak
- Oct 26, 2020
- 2 min read
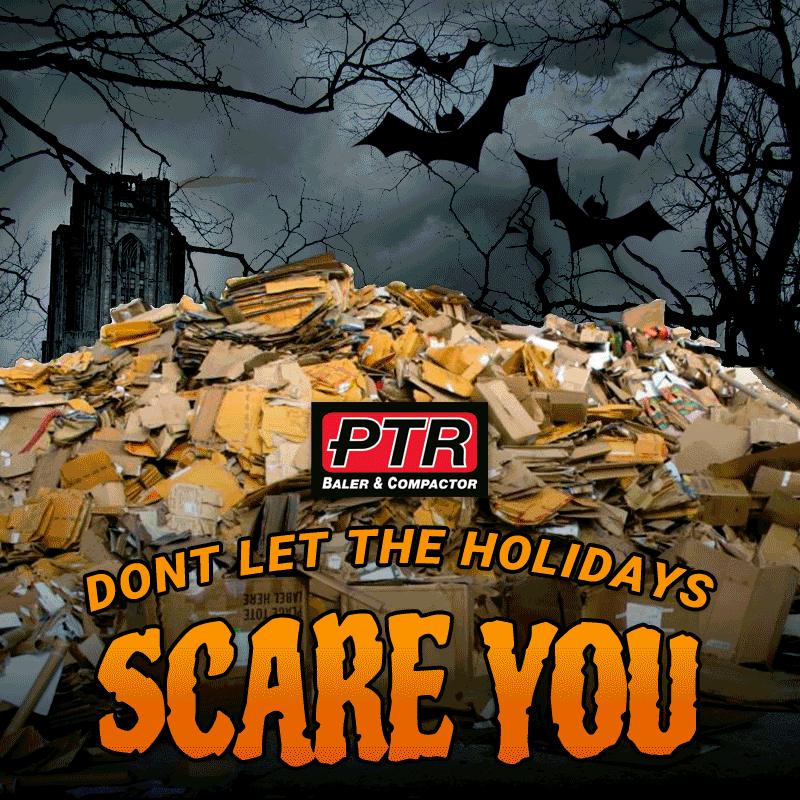
Be prepared for the increased holiday volume with PTR Service & Maintenance!
The holiday season is the busiest time of year for most retail businesses. Therefore, it’s also the busiest time of year for shipping companies and all companies who work with retailers. Making sure your waste and recycling equipment has been properly serviced is critical to ensuring an successful holiday season. The goal is for equipment to be functioning optimally, so there’s much less risk of cost-sucking downtime due as a result of service or repair. Our Preventative Maintenance and Service programs are a smart, cost-effective investment for your company.
What makes PTR Service & Maintenance different than our competitors in the industry?
PTR Services and Dispatch calls 24 hrs a day, 365 days a year
Provide engineering support (mechanical & electric)
PTR submits quotes for quotes beyond the NTE’s
Provide daily support similar to a 3rd party software management
99% rate of arrival on or before scheduled ETA
80% first time completion rate for service
Provide Engineering Support (Mechanical & Electric)
Provide Support similar to a 3rd Party Software Management on a daily basis
Manage 3rd Party Insurance Certificates
Service Call “Storage” for OSHA / Service EOL Guidance
Another major benefit of working with PTR for your baler and compactor service, repair and maintenance is that we manage our Service Truck inventory to be sure they are as accurate as possible. Additionally, all subcontractors inventory is reviewed to meet the same standards. That way we have what you need, when you need it. We also provide safety inspections for each and every service call we attend.
Because we are a manufacturer, we have access to all parts. Many of them are readily available at our facility. We’re able to pass these savings on to you, saving you time and money! You can view all electrical, mechanical and hydraulic parts at parts.ptrco.com.
When we perform a Preventative Maintenance check, our expert technician will address the critical systems and structures of your unit, including the following:
Evaluate overall equipment condition.
Verify that all safety decals are in good condition.
Test and verify the operation of safety features.
Thoroughly inspect the cylinder welds and seals.
Grease all fittings.
Inspect all hoses and crimps.
Inspect all hose clamps and tighten as needed.
Inspect motor for signs of wear or end of life conditions.
Inspect pump for leaks or signs of failure.
Inspect oil level and general condition.
(Optional) Perform oil analysis by an independent laboratory.
Operate gauge and verify that there are no leaks and operational.
To see the complete list of items addressed, click here.
Programs can also be customized to best suit your company’s needs. Some popular add-ons include:
Replacing up to 5 gallons of Hydraulic Fluid
Replacing Safety Stickers
Replace two main hydraulic hoses and fittings
Replace start/stop button
Replace key switch
Key Guard Installation
Call us to schedule your maintenance appointment for the busy Holiday Season! (800) 523-1155